Eine saubere Grundlage für individuelle Lackierprozesse
Aktuelle BvL-Anlagenprojekte überzeugen für das Anforderungsspektrum zur PaintExpo
Im Bereich der industriellen Reinigung zur Vorbereitung auf individuelle Lackierprozesse hat der Anlagenhersteller BvL Oberflächentechnik in jüngster Zeit verschiedene Lösungen für Kundenanforderungen unterschiedlichster Art umgesetzt.
Umfangreiches Reinigungsverfahren im hohen Durchsatz
Innerhalb des Produktionsprozesses reinigt ein großer europäischer Hersteller von Hausgeräten verschiedene Backofenkomponenten mit insgesamt drei neu installierten Durchlaufanlagen YukonDAH in Kombination mit einem bauseitig vorhandenen Hängeförderersystem. Die Bauteile müssen nach dem Waschen und Trocknen frei von Öl, Schmutz und Restfeuchte sein, was auch für gefaltete Kanten und weitere Hinterschneidungen gilt. Hierdurch wird eine optimale Vorbereitung für den nachfolgenden Emaillierungsprozess gewährleistet. In einem getakteten Verfahren erfolgen mit der 3-Tank-Anlage die folgenden Prozesse nacheinander: Reinigen, Vorspülen, Nachspülen, Abblasen und Trocknen. In jeweils einer der fast 30 Meter langen Anlagen wird ein Gesamtdurchsatz von ca. 1,6 Mio. gereinigten Backofenkomponenten pro Jahr ermöglicht. Zur Energieeinsparung wird mit Hilfe des Abluftmanagements die Abluftmenge minimiert und durch die Strömungsoptimierung wird die notwendige Heizleistung reduziert.
Bedarfsorientierte Reinigung schwerer Metallteile vor der Lackierung
Ein weiteres aktuelles Anlagenbeispiel steht kurz vor der Auslieferung zum Kunden. Zur Vorbereitung auf die nachfolgende Lackierung werden Planetengetriebe, Drehwerke und Winden für ein großes metallverarbeitendes Unternehmen mit einer Taktanlage PacificDTH gereinigt und phosphatiert, nachfolgend gespült und im Umluftverfahren getrocknet. Angebunden an das kundenseitige Hängeförderersystem durchfahren die Bauteile die Anlage. Die beiden oszillierenden Spezialdüsensysteme, die mit dem Wasch- und Spültank separat verbunden sind, sorgen innerhalb derselben Kammer für zuverlässige Reinigungsergebnisse und Oberflächeneigenschaften. Die Großanlage ermöglicht die Behandlung großvolumiger Bauteile mit einer Kantenlänge von bis zu 3 Metern. Die zusätzliche Isolierung von Rohrleitungen, Filtern und Tankabdeckungen sowie der Einsatz eines Dampfkondensators sorgen für eine signifikante Reduktion des Energieverbrauches.
Sensortechnik Libelle sorgt für vorausschauende Wartung
Bei beiden Anlagen sorgen verschiedene Systeme der Libelle-Sensortechnik für eine dauerhafte Überwachung des Reinigungsmediums und reduzieren so den Wartungsaufwand.
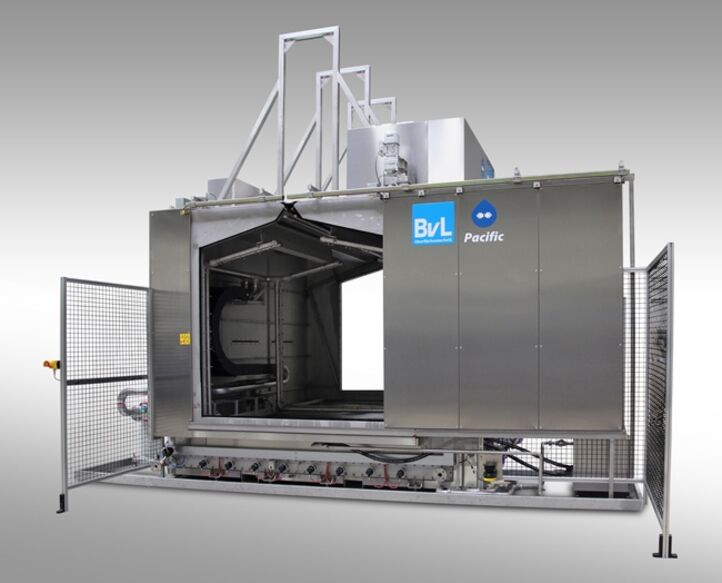
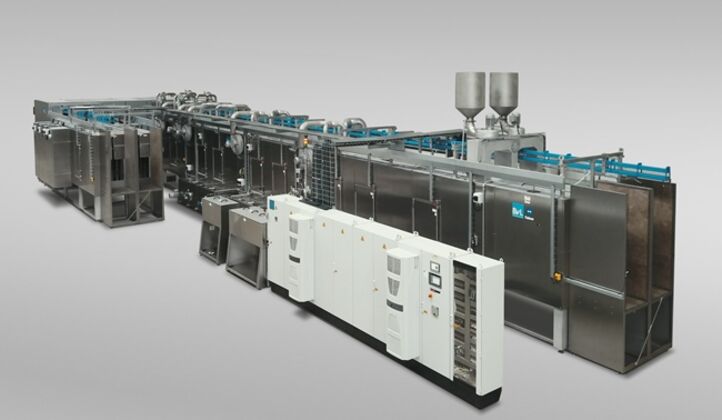
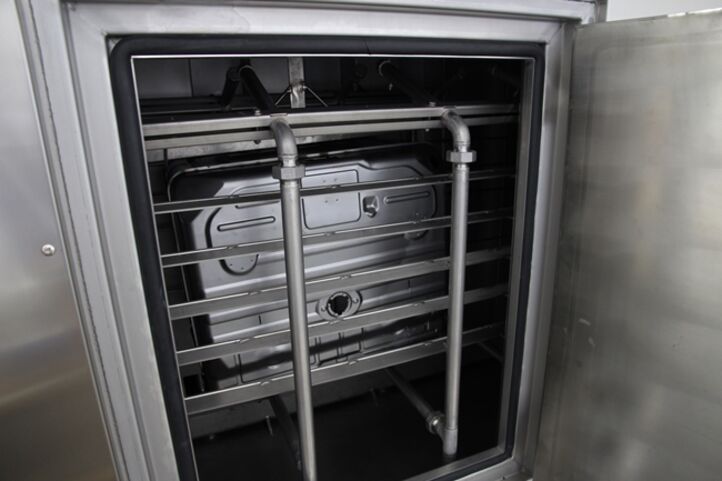