Clean vehicle parts for the EV sector
Components for structural reinforcement of EV front sections
Anyone opening the hood of an electric vehicle will be greeted by an empty trunk. No longer needed by the drive train, the engine is absent – and with it a certain amount of stability and protection for passengers.
To ensure passenger safety and the integrity of the battery in the event of a collision, new and lightweight components made from aluminum or hybrid materials, for example, are therefore being introduced to give the chassis the necessary rigidity and mechanical strength. The front of an EV features an entirely new structural design plus reinforcement to compensate for the loss of the combustion engine.
Water-based cleaning as a key preparatory step before bonding and welding work
To ensure that these advanced new components can be bonded and welded successfully, thorough water-based cleaning beforehand is an essential step. Components must be free from grease and staining. In addition, all other hollow sections that are used for reasons of reducing weight or noise emissions must also be thoroughly cleaned – both inside and out.
A wide range of challenges for cleaning in the EV sector
CEO and owner of BvL Oberflächentechnik GmbH Bernhard Sievering reports on the wide variety of challenges found in relation to parts cleaning for electric vehicles. “In the automotive sector, we’ve long experience as specialists for reliable and highly advanced cleaning solutions. And we’re equally well positioned to serve the needs of EV makers. These ‘new parts’ can be cleaned with a batch or continuous cleaning process. BvL systems also offer efficient and reliable processes for cleaning other electric vehicle components, including battery housings and a wide range of parts used in the power train and power electronics.”
A practical example: cleaning long vehicle body parts
For cleaning especially long body parts, such as extruded sections, one obvious choice would be the dual-tank Ocean 1600 RW cleaning system from BvL with a custom usable height.
In this case, BvL engineers designed and built a special-purpose workpiece carrier, to which the body parts – up to 2,200 mm in length – are fixed in an upright position to ensure full access to the areas needing cleaning. A lifting table is used to raise the workpiece carrier from floor level to the machine height. After cleaning – using a jet spray method – the parts are rinsed with DI water to reduce mineral and cleaning agent residues before painting.
Parts are then dried by a circulating air drying system with a blower nozzle covering the entire usable height. Thorough drying of parts on all sides is ensured by the turntable plus workpiece carrier rotating as it passes the drying nozzle.
The surface tension standard of ≥38 mN/m required for paintwork is reliably achieved. Paint adhesion is guaranteed as long as system parameters remain stable.
BvL Libelle products for improved process reliability
To analyze and monitor system parameters such as conductivity, pressure, and temperature, a wide range of sensors such as the BvL Libelle Fluid Control and Libelle Cleaner Control are utilized per batch. Measured values are recorded here by an integrated data logger. Libelle products ensure a high level of quality control and process monitoring.
The BvL Libelle Oil Control Solo measures part surfaces to guarantee that parts meet specifications for painting after cleaning. This portable device can be used to make quick decisions about part readiness for downstream processes.
BvL Oberflächentechnik GmbH is one of the largest suppliers of water-based industrial cleaning systems in Germany. As a system partner, BvL offers comprehensive customer solutions through integrated services – from compact washing units and filtration/automation solutions to complex large projects with process monitoring, always complemented by reliable service. BvL currently has around 160 employees. In terms of exports, the company has expanded its position on an international scale, and can rely on an extensive sales and service network in 19 countries.
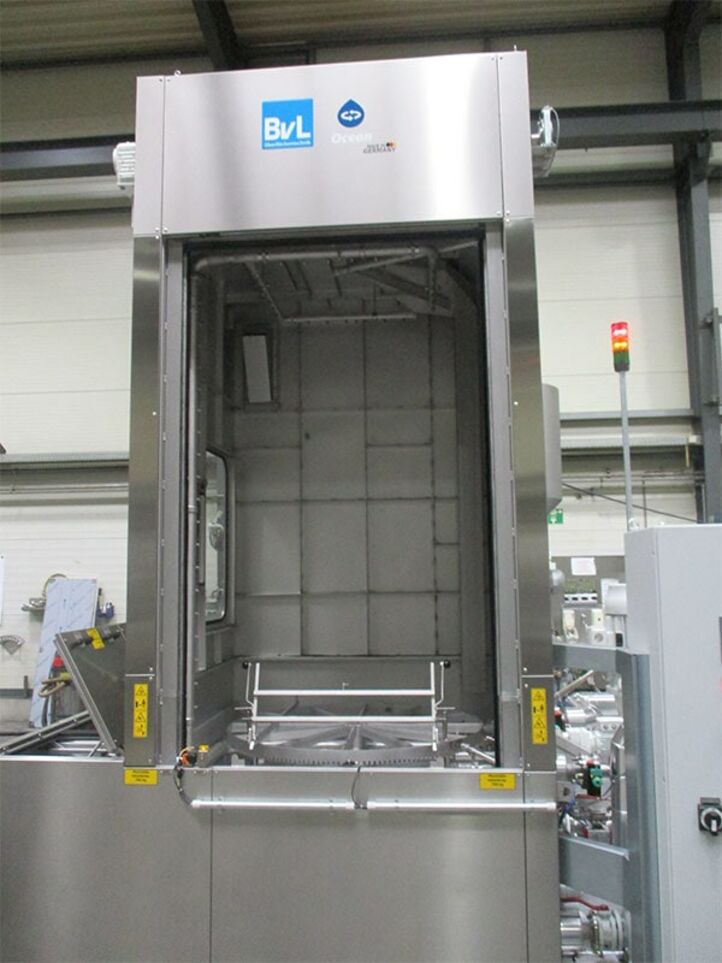
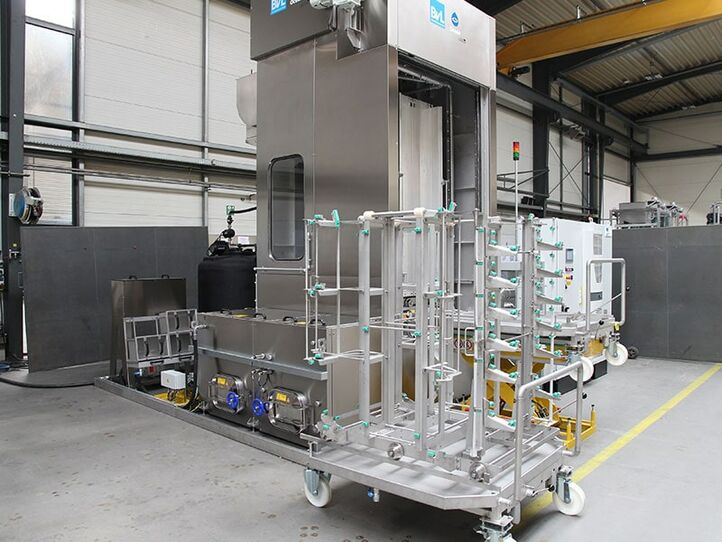