Programming and control
Intelligent systems
Fields of application
System control and programming can be adapted and customised to meet specific customer requirements. This facilitates processes, links interfaces and systems and allows cleaning systems to be integrated into existing production and manufacturing lines.
- standardized controller for operators
- prevention of operating errors
- optimized cycle times
- linked upstream and downstream operative facilities
Available features
- pre-selection of washing programs, freely selectable treatment parameters
- simplified washing program selection at the push of a button
- interface programming
- integration of third party applications
- customer specific programming and compliance with programming languages
- communication with other systems and production data acquisition
- visualization through touch panel, key panel or panel PCs
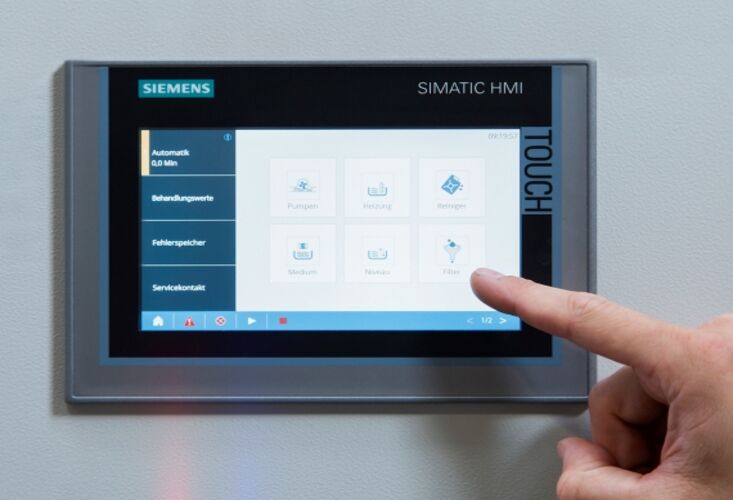
Handling and automation
Quick and ergonomic
Fields of application
Handling systems facilitate the movement of workpieces. They provide easier transport of the cleaned parts and shorten ancillary system times. Ergonomic factors such as ideal working height or weight transfer also play an important role. Automated transport systems are used for large batches, for production lines with pre-set cycle times or for production using one piece flow. These transport systems can also be designed as intelligent systems so that the correct washing prgram for each batch of parts could be selected directly through a barcode query, for example.
- reduction of time required for loading and unloading the system
- reduction of personnel time
- increased throughput
Available features
- integration of the workpiece carrier
- parts feeding carriage
- folding lifting table
- cross-movement table
- bridge loader
- roller conveyor (with workpiece buffer, if required)
- conveyor systems, conveyor belts
- robot and manipulator systems
- positioning systems
- complex, fully automated transport systems with identification systems for workpiece tracking
- linking of several cleaning systems
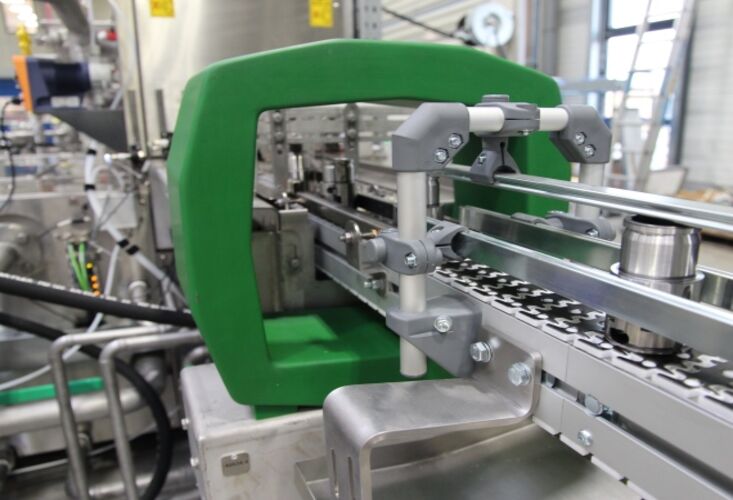
Increased cleaning capacity
Reaching individual requirements of cleanliness
Fields of application
The cleaning systems are individually customized or adapted to comply with strict cleaning requirements. This increases the cleaning capacity and sustains the required quality of the bath for an extended period of time. The required cleaning capacity can therefore be ensured even for complex components with difficult geometric shapes.
- permanently ensuring the cleaning capacity
- meeting high cleaning requirements
Available features
- selection of the correct cleaning chemicals
- adaptation of the nozzles or integration of additional nozzle systems
- flood washing
- vacuum flood washing
- ultrasound cleaning
- increased pump rating
- water softening system
- manual spray lance or high-pressure cleaning lance
- filter techniques such as nominal or absolute filters
- full stream filters (single and twin reversing filters)
- automatic return flow filters
- magnetic bar inserts
- micro filtration
- degaussing systems
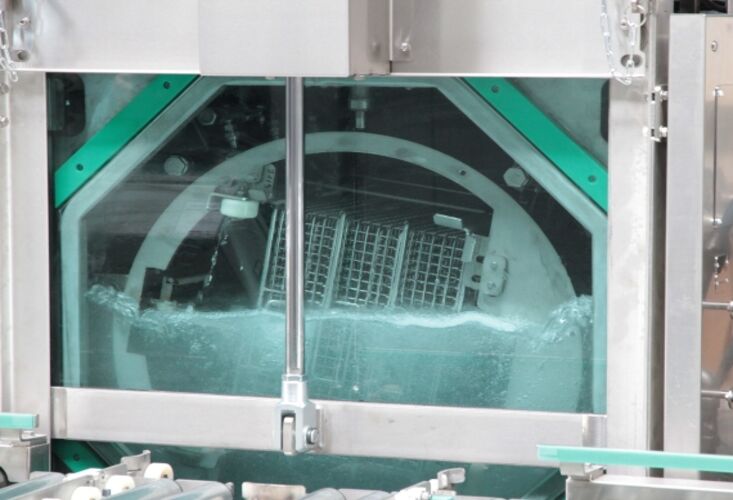
Workpiece holders suitable for washing
Link between workpiece and cleaning system
Fields of application
The workpiece holder is the link between a workpiece and the cleaning system, influencing the end result, duration and cost of the cleaning. An optimally-selected workpiece holder securely holds the workpiece, allows the best possible accessibility for the cleaning medium, accelerates drying and minimizes spread. Loading and unloading have to be simple, and if required, the workpiece holder also has to be suitable for use as a transport container in production.
- meeting the requirements for cleaning and drying
- safety of the component during the cleaning process
- efficient process guiding with minimal setup work
Available features
- parts baskets with standardised accommodation systems
- development of adapted workpiece holders – for sensitive parts or complicated geometric shapes
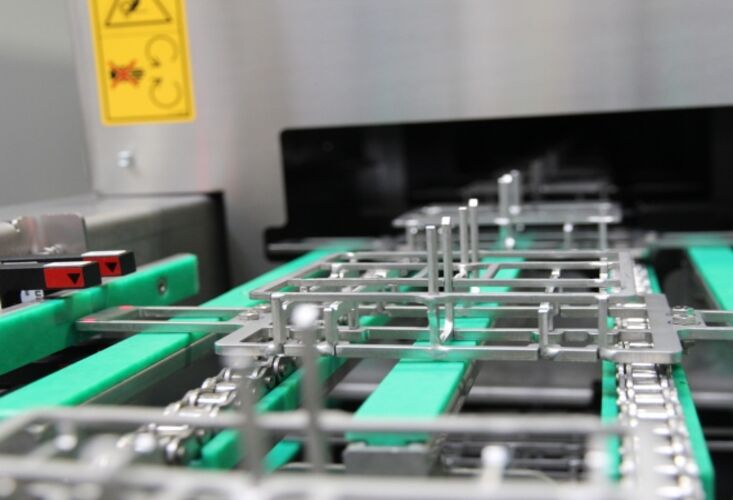
Increased bath life
Reduce bath changes
Fields of application
In the production process, bath changes are non-productive times when no cleaning can take place. Costs of manpower, cleaning agents, disposal and reheating of the bath are also incurred. The cleaning capacity of the bath can be extended by proactively removing dirt from the bath during the process and immediately compensating for the loss of water and cleaning agents.
- increased system availability
- minimisation of costs
Available features
- tank rinsing – to prevent deposits
- cascade guiding
- re-dosing of cleaning agents
- centrifuge
- plate phase separator
- band and return flow filters
- water softenting and reverse osmosis systems
- evaporator
- mechanical discharge systems
- Libelle – bath monitoring to avoid spread

Saving energy
Reduce operating costs
Fields of application
Cleaning is one of the energy-intensive processes in manufacturing, due to the great consumption of thermal energy. The energy consumption of a cleaning system has an immediate effect on the manufacturing costs of parts. The BvL energy saving packages use two adjusting screws to reduce energy: the reduce the energy required for cleaning as well as energy losses of the system.
- lower operating costs
Available features
- determining the optimum bath temperature
- determining the optimum cleaning period
- steam condensers and mist eliminators
- flow-optimized drying (for continuous processing systems)
- exhaust management
- insulation
- use of highly energy-efficient motors
- heat recovery
- bath heating systems: electric, gas, tube nest heat exchangers, heating coil, integration of technical heat or external heat
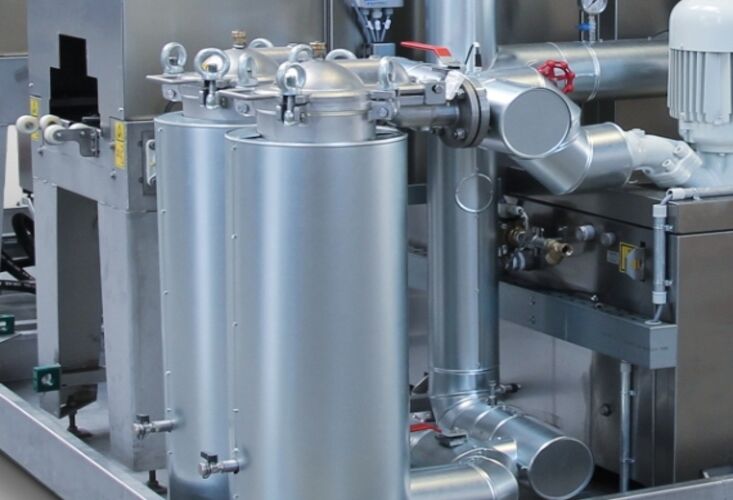
Emergency strategies and fail-safe operation
Highest machine availability
Fields of application
In many production facilities, the cleaning system is the "bottleneck" through which the components of several processing centers have to pass before they can be used in additional processes. Therefore, it is important to have a system availability of virtually 100%. A safety concept and the selection of suitable components minimize the probability of failure. The emergency strategy covers options for at least partially maintaining the cleaning operation despite possible malfunctions, e.g. through the use of modular, individually controllable systems or through components working in parallel or redundantly to at least partially compensate for the failure of individual components.
- increased system availability
- ensuring cleaning capacity
Available features
- risk assessment
- remote diagnosis
- regular service and maintenance
- development of an emergency strategy
- creation of redundancies
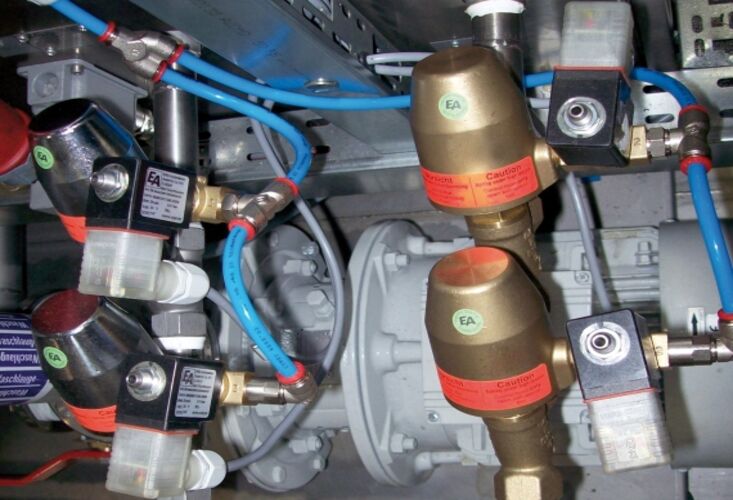