Efficient Immersion cleaning system for rotor production in the e-mobility sector in a fully automated line
A leading machine tool manufacturer has recently made a landmark investment by integrating two state-of-the-art immersion cleaning systems into a newly developed fully automated production line for electric motor rotors. Given the high cleanliness requirements in the e-mobility sector, this investment is an important step in ensuring that components meet stringent quality standards.
The end customer for these high-precision components is one of the largest car manufacturers in Germany. The machine tool manufacturer has opted for the Atlantic cleaning system from BvL Oberflächentechnik GmbH. This choice underlines the manufacturer's confidence in the outstanding quality and performance of BvL's products.
Cleaning systems integrated into production island with robots
These pioneering immersion cleaning systems have been optimally integrated into a production island with robots in order to maximize production efficiency and quality. The rotors, which are produced in six different types for electric vehicles, are subject to very high cleanliness requirements - they have to be cleaned of dirt particles such as chips and cooling lubricants.
Concept with two systems for pre-cleaning and fine cleaning
The first cleaning system is used for pre-cleaning after mechanical processing, while the second system is used for fine cleaning after the ECM process (electrochemical metal processing).
With a cycle time of 156 seconds per batch (four components), the Atlantic systems offer an effective multi-stage immersion cleaning solution with ultrasonic support. The workpiece carriers are immersed in the cleaning tanks using an automated gantry transfer unit, with the oscillating lifting movement of the workpiece carrier supporting the cleaning process.
The pre-cleaning system comprises three immersion tanks for cleaning and rinsing as well as a downstream heated circulating air dryer. The ultrasonic device in the cleaning tanks ensures an efficient and gentle deep cleaning effect. The fine cleaning system has an identical design, but has integrated vacuum drying instead of circulating air drying. This ensures 100% drying of the rotors at the end of the line.
Particular attention was paid to the workpiece carriers. These were specially designed by BvL to enable optimum alignment of the components for cleaning and at the same time to be suitable for robot loading and unloading.
Smart Cleaning functions enable predictive maintenance of the cleaning system
To optimize the maintenance process, the systems have the innovative Smart Cleaning function from BvL. The bag filter consumption forecast reports the current contamination status of the bag filter and indicates when the filter needs to be changed. Predictive maintenance and stocking of spare parts is therefore safe and easy. The operator can schedule the filter change efficiently into the production process.
The steam condenser of the cleaning system is easily accessible for maintenance via a walk-on maintenance platform.
BvL ensures optimum interface communication of the cleaning system by connecting it to the hall network and thus seamlessly integrating the cleaning system into the overall production process. Important production data can be exchanged and monitored in real time, resulting in more efficient planning, control and monitoring of the cleaning processes.
The Atlantic immersion cleaning system from BvL is not only used in the field of electromobility, but also in a variety of precision industries with high cleanliness and capacity requirements, such as hydraulics, pneumatics, optics, electronics, aerospace and the coating industry. The systems are scalable and can be flexibly adapted to individual requirements.
In order to determine the best possible cleaning solution, BvL carries out extensive test cleanings with original components in its in-house technology center. This ensures that the cleaning processes are optimally matched to the cleanliness requirements of the components.
BvL Oberflächentechnik GmbH is one of the largest suppliers of aqueous-based industrial cleaning systems in Germany. As a system partner, BvL offers comprehensive customer solutions through integrated services - from small, compact washing systems to filtration and automation solutions through to complex, customer-specific large-scale projects with process monitoring; always complemented by reliable service. BvL currently employs around 160 people. In export, the company has expanded its international positioning and can rely on an extensive sales and service network in 20 countries.
Contact:
BvL Oberflächentechnik GmbH
Grenzstr. 16
48488 Emsbüren
Tel.: +495903 951-60
Press release:
Christine Brühöfner
Marketing
Tel.: +495903 951-509
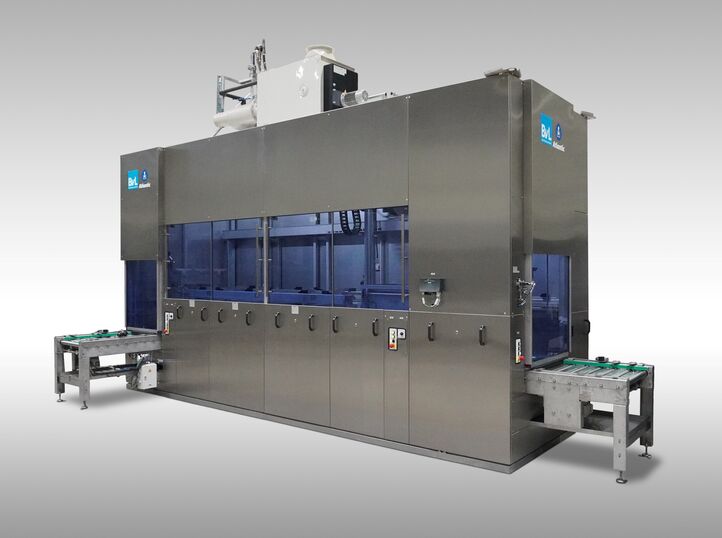
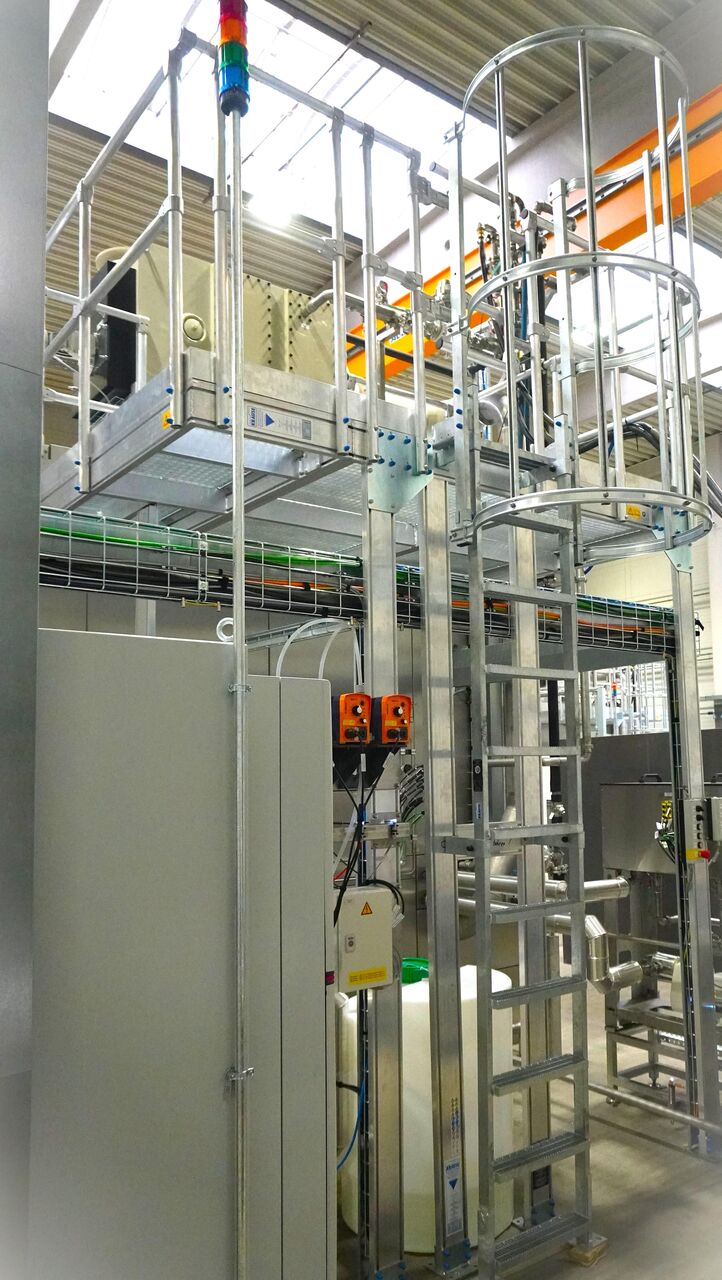
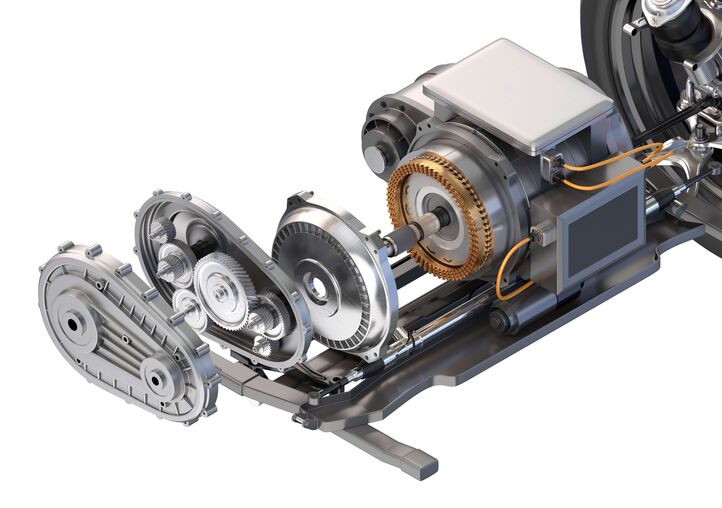