Fully automated cleaning system with pick and place system
Fully automated cleaning system with pick and place system
A fully automated cleaning system with pick and place system increases productivity and efficiency. The system no longer has to be loaded and unloaded manually and provides a high positioning accuracy with fewer processing errors.
A Dutch manufacturer of molded parts for the automotive and electronics industries, the medical sector and general industrial equipment selected the BvL Yukon cleaning system for thorough cleaning of its stamped parts in a fully automated process.
Some key prerequisites had to be met to ensure smooth integration of the cleaning system into the fully automated process chain. Not only the high cleanliness requirements played a crucial role for this application. A short cycle time of the cleaning system was also required to ensure the required speed in the production flow. This meant that specific times and quantities had to be considered during the planning the cleaning system. The starting quality of the workpieces and the requirements for further processing required optimum interface communication, as this was the only way to optimally integrate the system with the upstream and downstream production processes.
Fully automated cleaning process
The stamped parts come directly from the forming process, pass through the cleaning system and are then packaged. The entire process is supported by a pick and place system. The cleaning system therefore has to have a particularly short cycle time and high throughput to allow for integration in the fully automated process. Because the stamped parts are subsequently packaged, the cleaning process must not leave any stains and the workpieces have to be absolutely dry. The manufacturer chose a powerful Yukon continuous cleaning system from BvL Oberflächentechnik in Emsbüren (Germany). The Dutch manufacturer already has several BvL cleaning systems in operation and appreciates the competent and personal support.
“Our customer knows that we look at their entire production process and tailor our systems to their requirements,” reports owner and Managing Director Bernhard Sievering. “I have to say that I am also very proud of our team who always work closely with the customer, from project planning to design engineering and manufacturing. With our international sales and service network, we can ensure that we are always close to our customers on the international market. We also always have a native speaker on site. In the Netherlands, we worked with De Ploeg Techniked B.V. from Helmond. The owner, Mr. Cock de Jonge, ensured a close exchange with our Dutch customer.”
High throughput and efficient flow of materials even for varying components
The BvL Yukon cleaning system is an optimum inline solution for efficient material flow at high speed in the production line. The cleaning system achieves a particularly short cycle time of only 1 second per component. The conveyor belt on this machine has six tracks, allowing the pick and place systems to load and unload six parts simultaneously while the conveyor is running. The overall system is designed to ensure optimum positioning accuracy, even for different components. The adjustable throughput speed allows for efficient processing. This can be used to influence the cleanliness level of the components and also makes it possible to address different cleanliness requirements for varying components – a crucial aspect for the Dutch manufacturer of molded parts. Initially, this system will be used for cleaning components from stamping processes for coffee machines, with other stamped parts to follow later on.
Customized cleaning and drying process
The stamped parts pass through the successive treatment zones of the Yukon cleaning system in a continuous cycle. The conveyor belt transports the components from the intake zone to the cleaning zone, where they are cleaned evenly and all around. Here, the components move past a fixed nozzle system. The cleaning nozzles are individually aligned to specifically target the workpieces, providing thorough cleaning even in hard-to-reach areas to meet the manufacturer’s high cleaning requirements. The components are rinsed in the subsequent rinsing zone and then dried with warm air in the blow-out zone. The now thoroughly cleaned, stain-free stamped parts can then be directly introduced into the downstream packaging process.
Smart Cleaning functions for energy savings, process reliability and predictive maintenance
BvL cleaning systems can be equipped with intelligent Smart Cleaning functions. The blow-off zone, for example, can be designed to be particularly energy-saving at the customer’s request. Controlling the exhaust air as a function of the humidity provides energy savings and ensures stable drying results.
The filter technology makes it possible to predict when the bag filter needs to be replaced. This makes predictive maintenance and stocking the spare parts easy and reliable. The operator can efficiently schedule the filter change within the production process because the period for the filter change is shown on the control panel.
The BvL Libelle Fluid Control reliably measures the level of contamination of the cleaning bath with high precision. Detailed information about the bath condition is crucial for ensuring reliable processes and optimum use of materials. BvL consequently uses Libelle Fluid Control in its cleaning systems as a standard.
BvL systems can additionally be equipped with the Libelle Cleaner Control. This system ensures that the cleaning agent concentration is kept at the correct target percentage at all times. The feature provides not only unmanned, precise and continuous measuring of cleaner concentration, but also automatically tops up the cleaning agent.
The Remote Service function protects against loss of production and provides support for operating or setting up the system.
Information available at AMB and Parts2clean in Stuttgart
BvL Oberflächentechnik will be exhibiting at the trade fairs AMB (September 13 to 17, 2022) and parts2clean (October 11 to 13, 2022) in Stuttgart and will be providing information on cleaning solutions and innovative concepts for different industries and requirements. Washing trials with original components can be carried out at the in-house technology center in Emsbüren. These trials determine the economically and ecologically ideal combination of plant technology, cleaning medium and program sequence for the specific customer.
BvL Oberflächentechnik GmbH www.bvl-cleaning.com
Contact:
BvL Oberflächentechnik GmbH
Grenzstr. 16
48488 Emsbüren
Phone: +49 5903 951-60
Fax: +49 5903 951-90
info@bvl-group.de
www.bvl-group.de
Press release:
Christine Brühöfner
Marketing
Phone: +49 5903 951-509
Fax: +49 5903 951-90
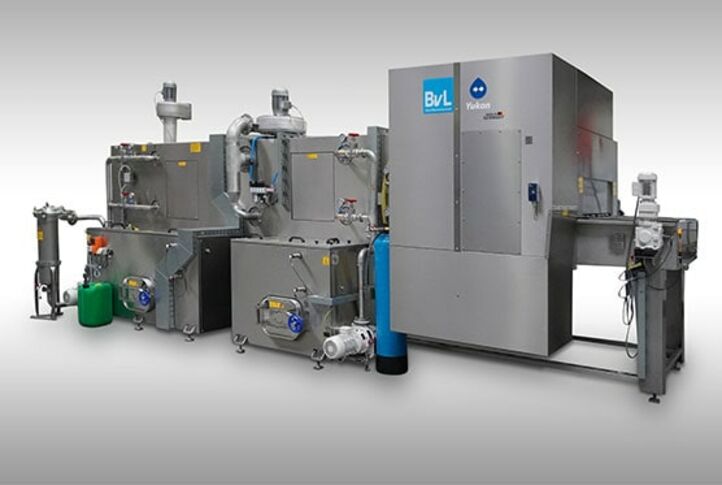
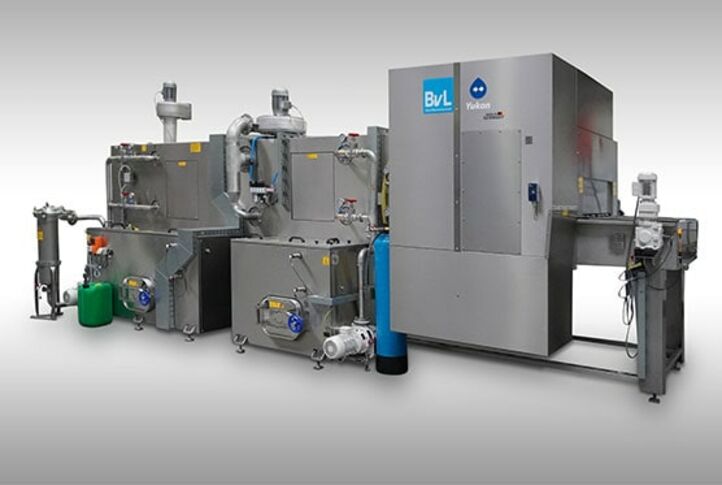
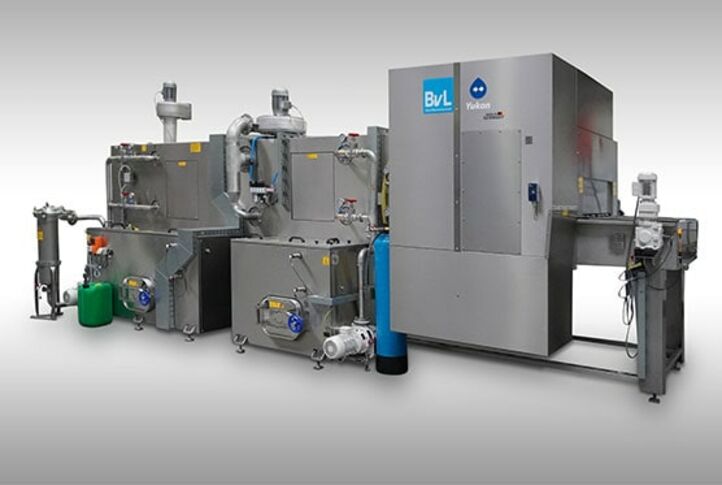
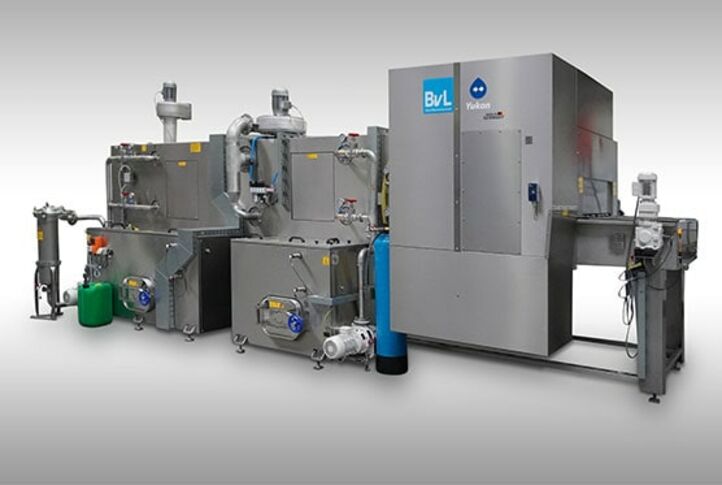