Modern cleaning solutions for optimum further processing and maintenance
Railway maintenance companies benefit from automated cleaning solutions
Railway components are exposed to extreme loads and heavy parts with their complex shapes consequently require intensive cleaning. Thorough cleaning is the only way to allow all downstream work such as maintenance, repairs, painting or quality and crack testing to be carried out.
To meet the current requirements for modern production systems and automation in this field, a number of maintenance and repair companies rely on a cleaning system with maximum automation.
Dutch railway maintenance company cleans wheelsets with automated system concept
The main operator of the Dutch NedTrain railway workshop has been successfully cleaning wheelsets with the BvL Pacific cleaning system. In addition to stringent cleaning requirements, other key aspects were almost 100 % availability of the system and networking of all washing cycles with the owner's data interfaces. Wheelsets with and without gear housing are cleaned.
By implementing a pit installation, it was possible to link the BvL cleaning system directly to the local floor loader system. A special nozzle system is used to direct water evenly onto the components, ensuring reliable cleanliness even in hard-to-reach areas of the heavy wheelsets. A camera system on the control panel allows for extremely safe one-sided operation of the continuous cleaning system. Flexible cleaning of a variety of different wheelsets and the level of automation in particular provide an ideal solution for the NedTrain maintenance operations.
State-of-the-art cleaning of drive bogies and wheel bearings in Austria
The maintenance workshop of an Austrian railway company was also looking for a fast and economical cleaning solution. They chose two cleaning systems from the German manufacturer BvL Oberflächentechnik GmbH in Emsbüren. After extensive washing trials at the BvL Technology Center, the customer selected the Pacific spraying system for cleaning bogies, wheelsets and frames and a Niagara spray/flood system for cleaning bearings and bearing housings. The Niagara cleaning system removes all traces of fine sand on bearings. This can prevent premature wear on axle bearings. The bearings are clamped into special washing baskets and cleaned in a washing chamber. While the parts basket rotates around the horizontal axis, intensive cleaning is provided by a special nozzle system with flat nozzles and by complete flooding of the cleaning chamber.
Very good cleaning results are achieved in both systems and the fully automated function makes handling particularly easy for the operators.
Component cleanliness thanks to adapted filters and bath sensors
The condition of the washing water and rinsing water is a key aspect for reliable, constant cleanliness of the cleaned parts. The medium is run through a belt filter to discharge solid particles. Tank rinsing in the pressure line of the washing and rinsing pump and a ring line above the tank base swirl up these solids in both tanks beforehand. Oil separation is additionally achieved by means of a plate phase separator with an integrated grease discharge device. The standard sensors in all BvL systems (Libelle Fluid Control) permanently monitor the level of contamination of the cleaning fluid by measuring light absorption. This allows the user to be alerted to an impending bath change in good time.
Environmentally friendly and energy efficient cleaning
After filtration, the wastewater is reintroduced into the system, which ensures a long service life while providing maximum savings on energy and water. Additional insulation of the pipes, filters and tank covers with a flexible material additionally reduces the discharge of thermal energy. In addition to reducing energy costs, this allows BvL systems to meet the relevant environmental protection requirements, ensuring a reliable investment for the future.
Personal consultations at Innotrans 2022
As an exhibitor at the Innotrans trade fair in Berlin from September 20 to 23, 2022, the company will be available to answer questions and provide explanations (hall 6.2, stand 430). In addition to cleaning bogies, wheelsets and wheel bearings, BvL also offers processing technology for cleaning hard-to-reach engines and for new components in production.
Find more information on the BvL cleaning solutions for railway systems at www.bvl-cleaning.com/rail
Contact:
BvL Oberflächentechnik GmbH
Grenzstr. 16
48488 Emsbüren
Phone.: +49 5903 951-60
Fax: +49 5903 951-90
info@bvl-group.de
www.bvl-group.de
Press release:
Christine Brühöfner
Marketing
Phone: +49 5903 951-509
Fax: +49 5903 951-90
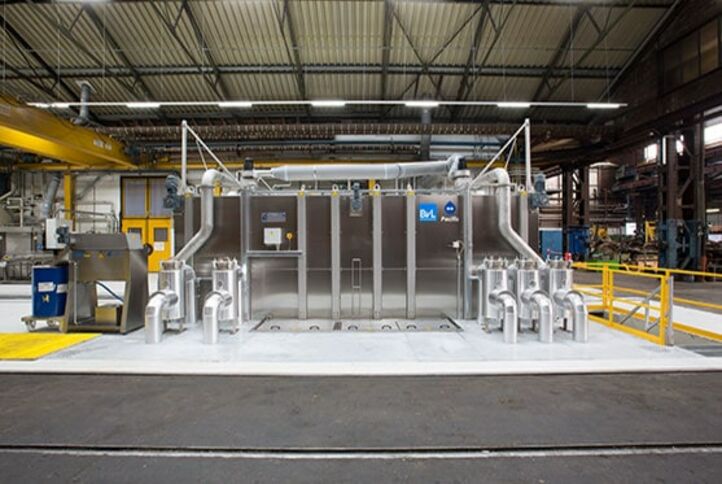
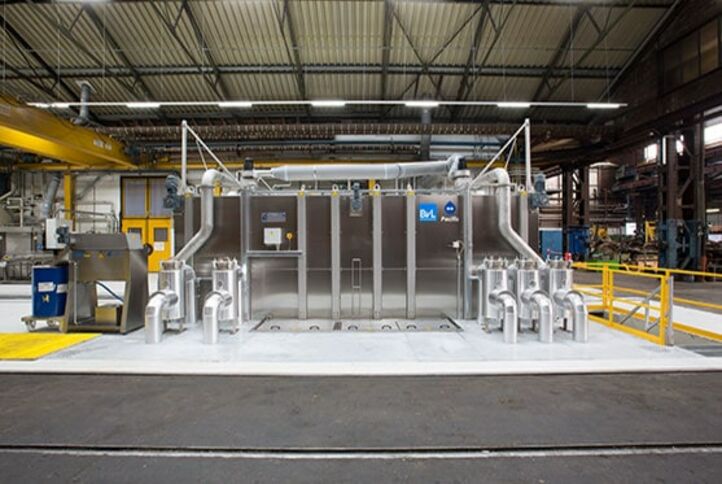
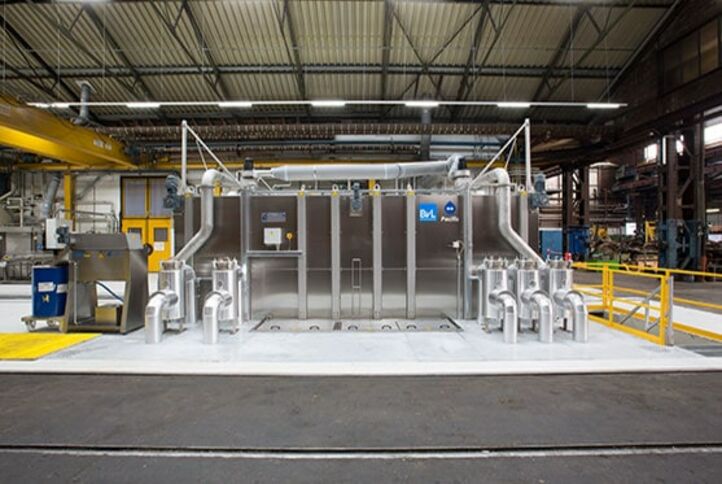
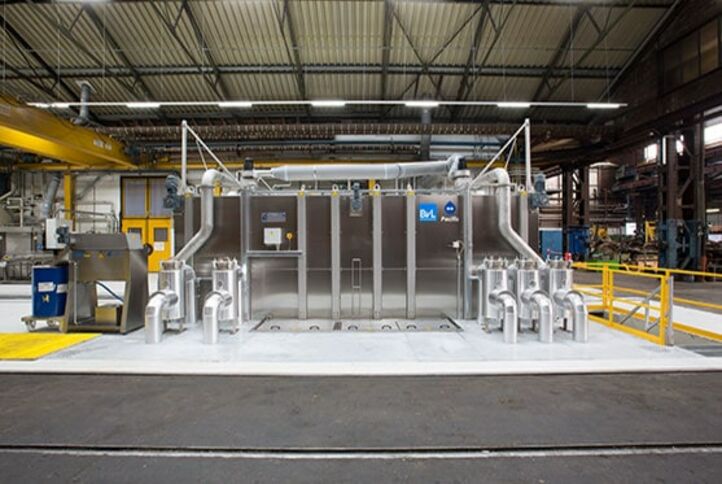
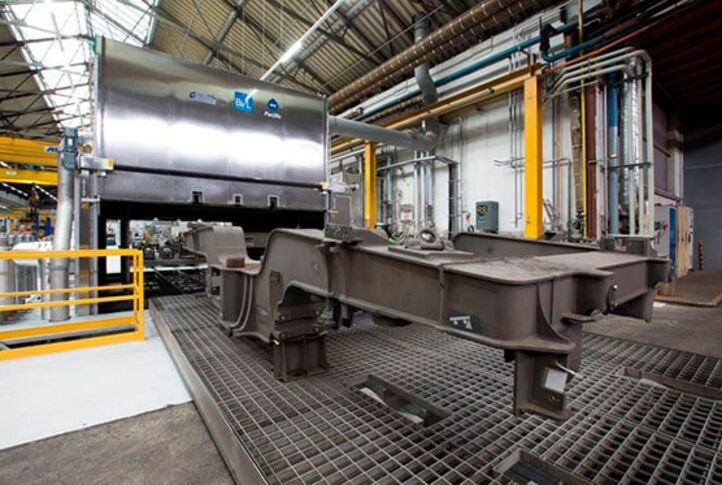
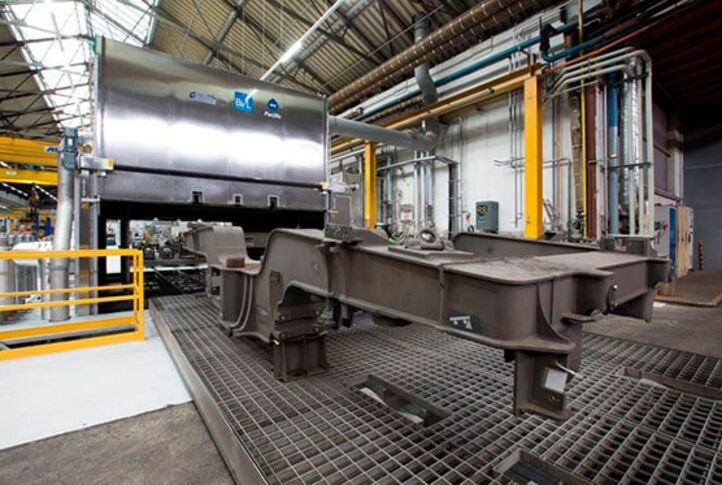
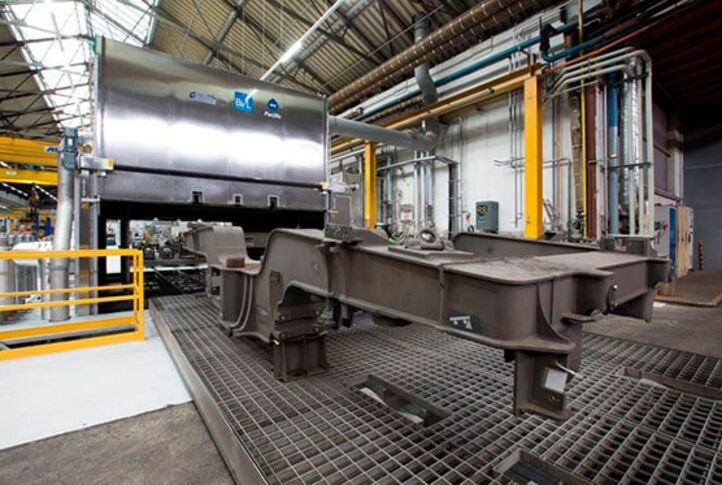
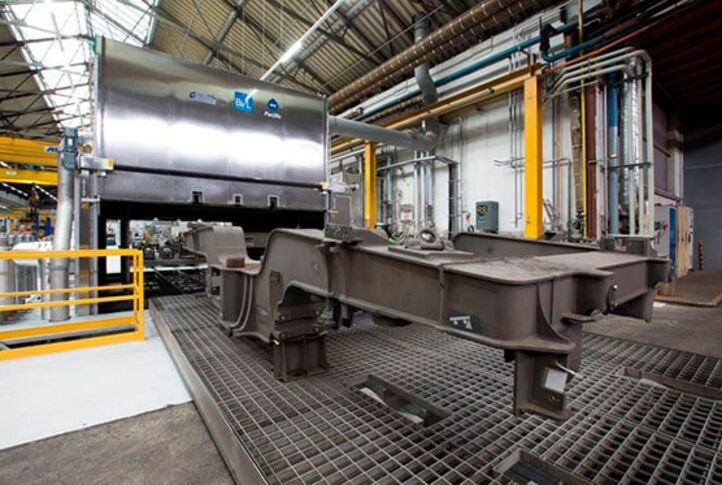
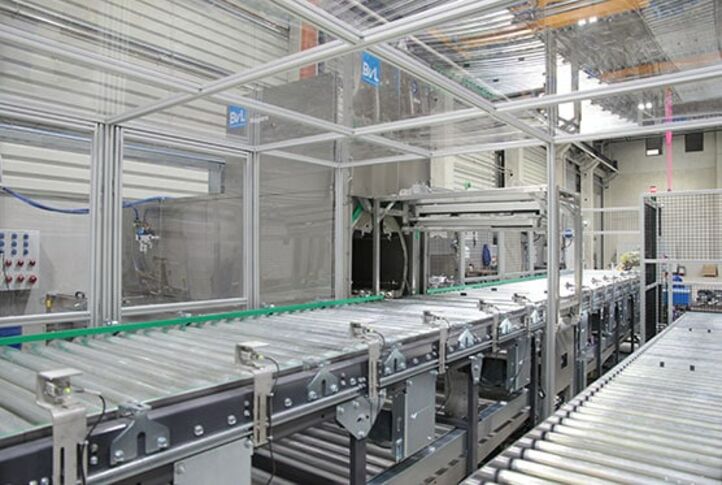
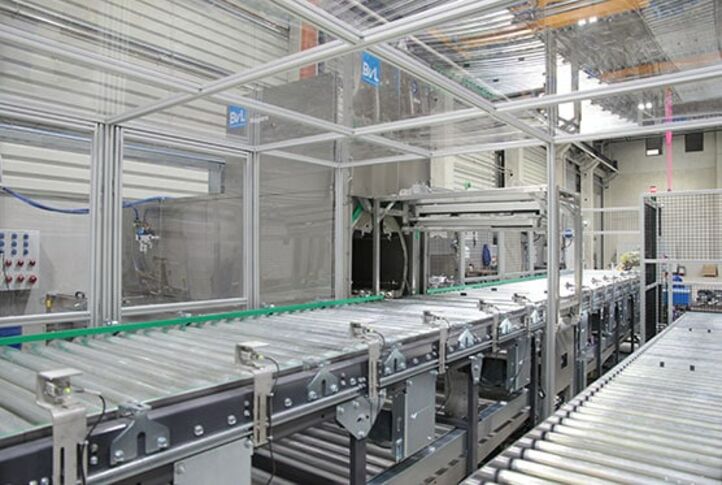
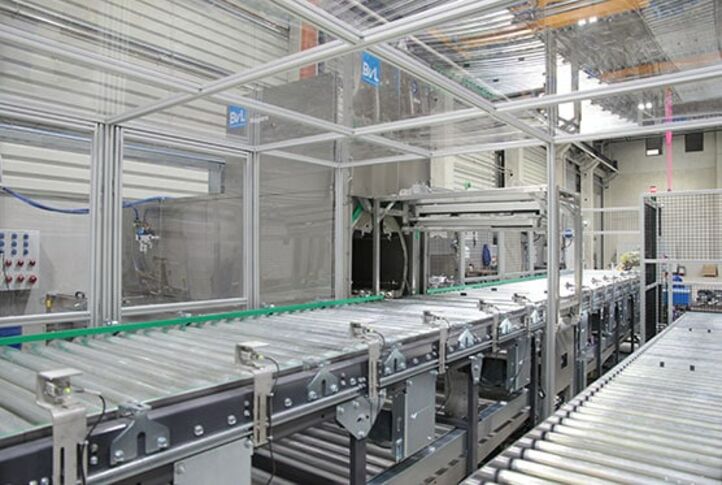
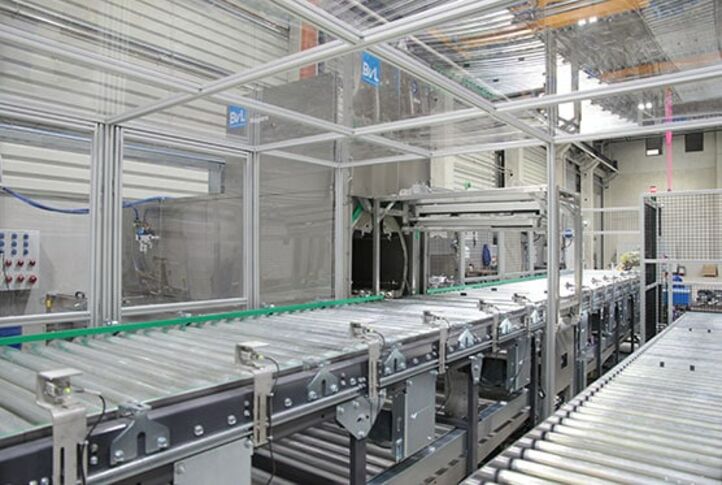