New parts reliably cleaned in all variants
BvL systems demonstrate high level of flexibility at Railway Workshop
A large range of different parts have to be cleaned during the production of any railway parts. BvL Oberflächentechnik manufactures systems which are ideally tailored to the specific application.
Heavy axles cleaned inside and outside
With a special OceanRW, BvL developed a solution for cleaning true heavyweights. A portal loader lifts new train axles with a weight of approx. 1,000 kg into the cleaning system and places them on prisms. While the axle rotates, a special nozzle system removes all machining residue from the outside and from the face-side threaded holes. Integrated blow-out nozzles allow fast, targeted drying.
Continuous system for new train wheels
The Yukon continuous system from BvL is also frequently used in the railway sector. In a specific application example, the system is used to clean new train wheels in a fully automated production line. The 650 kg wheels move through the system on correspondingly sturdy chains for targeted cleaning with a surrounding nozzle frame. Any cavities are then blown out specifically with drying nozzles and medium-pressure fans. A plate phase separator for oil separation and the modern filtration technology ensure a stable cleaning process.
Clean and dry axle boxes
Another variant of a Yukon continuous system is used for cleaning new axle boxes, for example. Several boxes are moved into the system at the same time. The continuous washing, rinsing and drying process reliably cleans different components with a weight of up to 12,500 kg every hour. In the system described, triple filters, Topline bag filters as well as an additional slant type filter ensure the reliable removal of contaminations from the washing and rinsing tank.
Efficient knowledge exchange at the BvL Railway Workshop
At the end of May, BvL invited experts from the railway industry to a workshop in Emsbüren, with the theme “Efficient and economical cleaning of railway components”. The guests from the fields of maintenance and manufacturing of new trains parts exchanged their extensive specialist knowledge with the BvL cleaning experts. The different processing technologies were illustrated with specific system demonstrations. Cleaning options for a large variety of different contaminations, for example on bogies, wheelsets, wheel bearings and motors, were explained. The informative knowledge exchange was completed with information on current trends regarding intelligent cleaning solutions with Smart Cleaning.
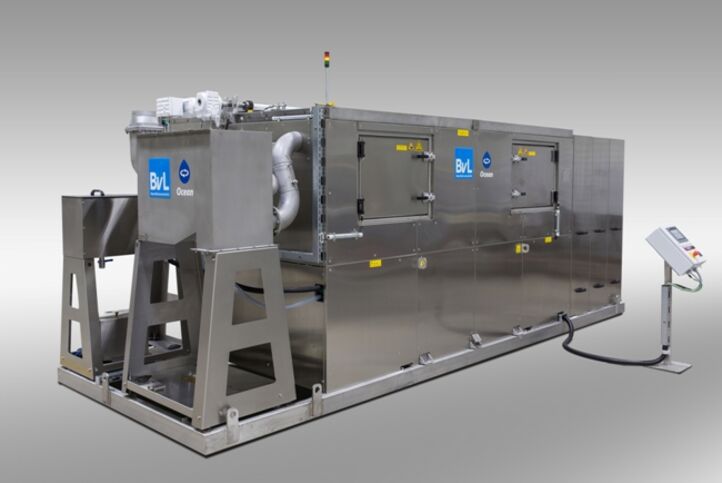
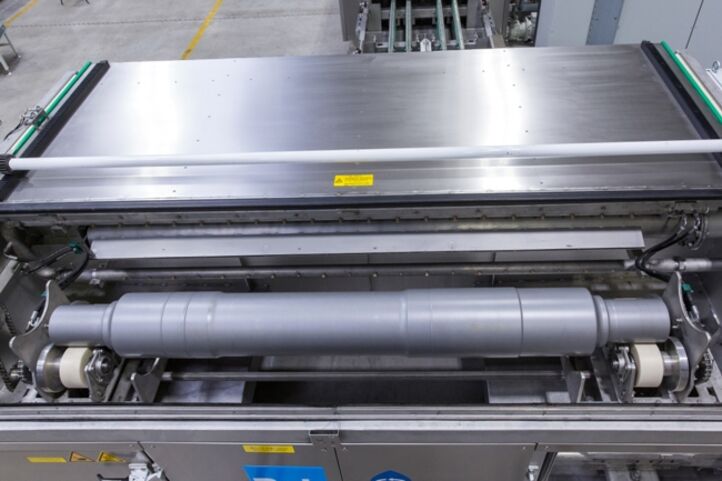
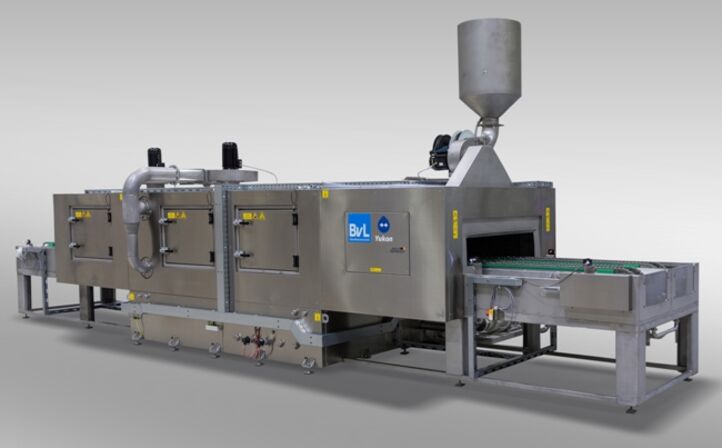