Efficient cleaning of transmission components after the production process: automotive supplier relies on automated cleaning system with gantry system
After the production process, transmission components such as spur gears, drive shafts, connecting shafts, axle drives and main gears must be thoroughly cleaned of the finest particles, chips, lubricants and oils. In addition to the high cleanliness requirements, the focus is naturally also on high productivity and efficiency for the cleaning process. A German automotive supplier recently opted for an automated basket washer with a NiagaraDFS gantry system from BvL Oberflächentechnik GmbH for precisely this application and is now benefiting from optimum and particularly efficient cleaning of its transmission components. The system meets all the requirements for thorough pre- and intermediate cleaning of a wide variety of components in a short cycle time.
Challenges successfully mastered
The decision to use the BvL cleaning system was influenced by several key factors. The automotive supplier was faced with the challenge of maintaining a cycle time of 15 seconds per component. The project planner benefited here from the cleaning system manufacturer's many years of experience. BvL had already designed several similar cleaning systems with automation in the past. These reference projects formed an ideal basis and BvL's experience and expertise played a key role in ensuring that this new cleaning system could be optimally tailored to the supplier's specific requirements. The automotive supplier's project planner appreciated the close cooperation with BvL during the entire project implementation and in particular the uncomplicated, direct implementation of his specific requirements for the automated cleaning system.
Solution: Two-axis gantry system with gripper system
Thanks to the two-axis gantry system with gripper system, the cleaning system has a high degree of automation and therefore a high degree of employee decoupling. The system can be operated with virtually no manual intervention. Errors are minimized, productivity is increased and a high level of quality assurance is achieved. The system is able to clean several baskets with a variety of different components in a short cycle time per wash cycle.
Insight into the cleaning process
The gear components are packed in stacked wire baskets and fed into the system via four loading stations. The gantry transfer unit picks up the baskets and transports them to the preparation station, where the basket stacks are collected for a cleaning batch. They are then transported to the cleaning system via a roller conveyor. All process steps - rinsing, cleaning and vacuum drying - take place in a single chamber. Thorough cleaning on all sides is carried out by a special nozzle system with a pivoting basket and subsequent flooding of the cleaning chamber.
Clever: Integrated floor roller cleaning station
Another highlight is the integrated floor roller cleaning station. This station cleans the bottom rollers of the basket stacks while the baskets with the components are in the cleaning chamber. This integrated process prevents the baskets and components that have already been cleaned from becoming soiled again.
Innovative smart cleaning technologies for greater process reliability
The BvL cleaning system is equipped with Smart Cleaning technologies. Maintenance prediction for the vacuum filter and consumption prediction for the bag filter enable predictive maintenance and optimized planning. The so-called Libelle Fluid Control measures the degree of contamination of the cleaning fluid and enables simple process control. This allows the customer to react quickly to changes and ensure constant component cleanliness. The insulation of the system components reduces the discharge of thermal energy, which leads to a reduction in energy consumption and therefore to cost savings.
BvL Oberflächentechnik GmbH is one of the largest suppliers of water-based industrial cleaning systems in Germany. As a system partner, BvL offers comprehensive customer solutions through integrated services – from compact washing units and filtration and automated solutions to complex large projects with process monitoring, always complemented by reliable service. BvL currently has around 160 employees. In terms of exports, the company has expanded its position on an international scale, and can rely on an extensive sales and service network in 20 countries.
Contact:
BvL Oberflächentechnik GmbH
Grenzstr. 16
48488 Emsbüren, Germany
Tel.: +49 5903 951-60
Fax: +49 5903 951-90
Press Release:
Christine Brühöfner
Marketing
Tel.: +49 5903 951-509
Fax: +49 5903 951-90
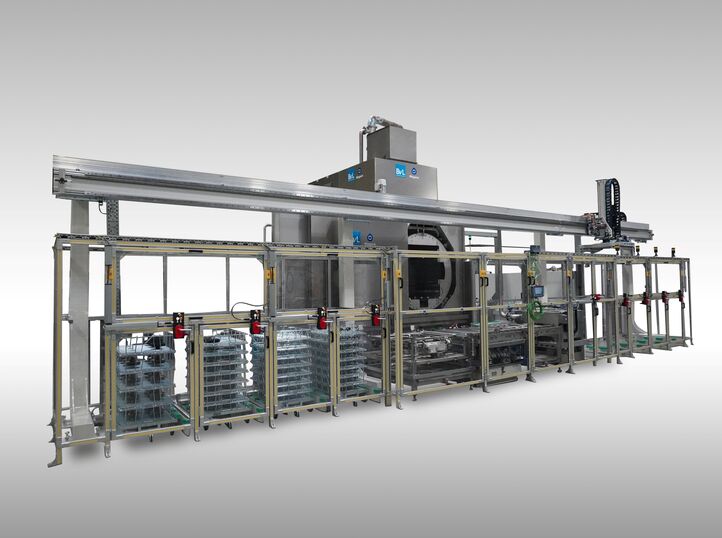
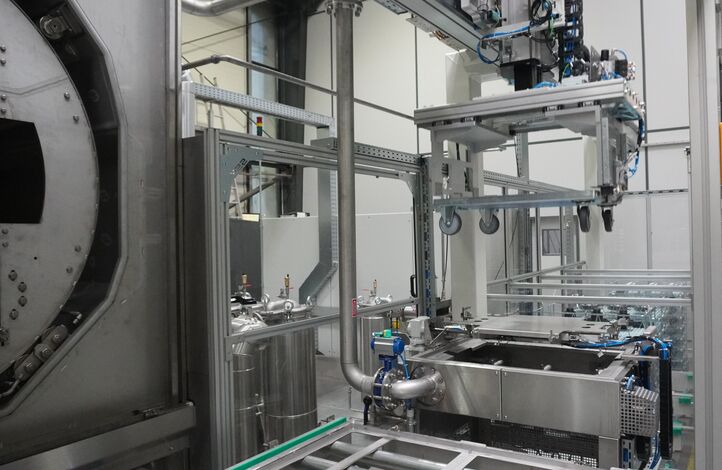
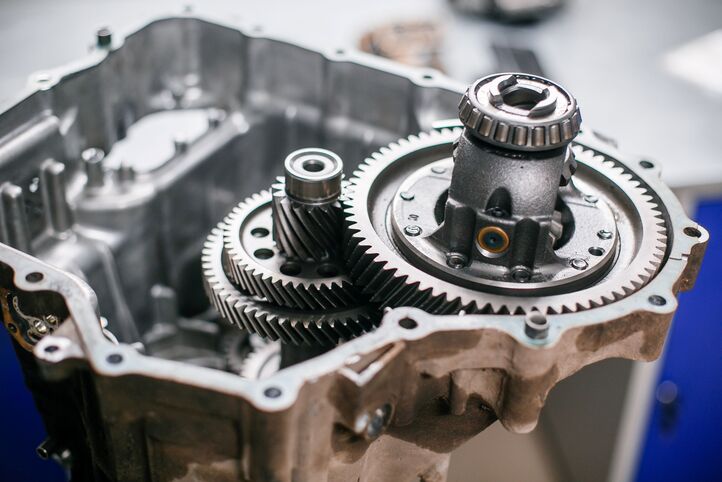