Reliable drying and cleaning of gearwheels with complex geometries
Even complex geometries, as on these gearwheels, are cleaned thoroughly. Subsequent separate and combined circulating air vacuum drying ensures complete drying in a fast and energy-saving process.
Cleaning large batches of bulk goods
Residue is easily removed from tightly packed small stop plates before annealing. This ensures a perfect heat treatment process and prevents rejects.
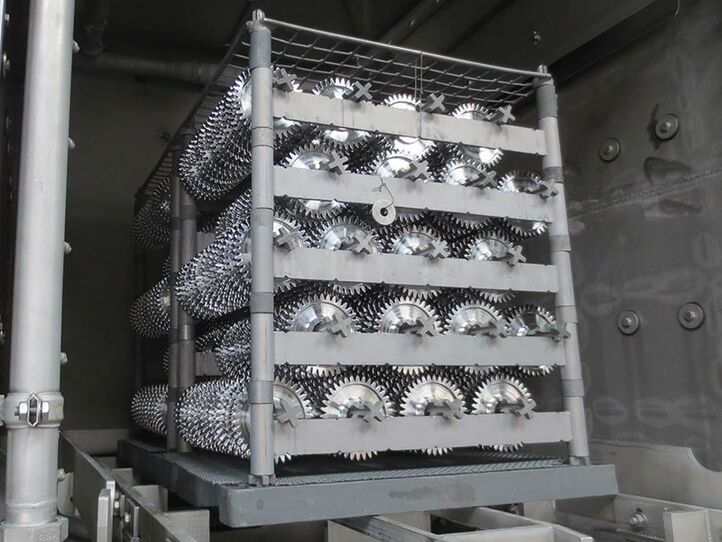
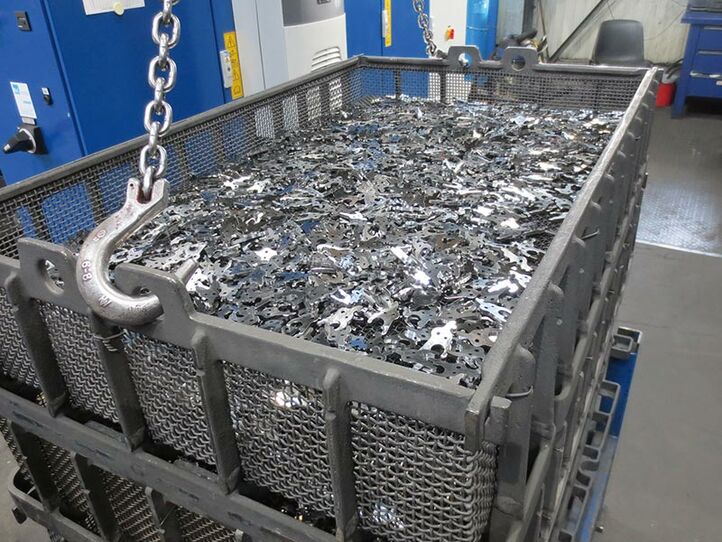