Parts cleaning is ready for electromobility
Parts cleaning is ready for electromobility
Electric cars are changing automotive production. The systems for manufacturing the new drive components have to be efficient and reliable, with parts cleaning remaining essential.
Whether building new factories for electric vehicles or converting existing facilities: General contractors supply car manufacturers with entire production lines for manufacturing gearboxes and motors for electric vehicles. Cleaning systems are a key component of this. They have to be equipped with the appropriate automation technology to achieve optimum integration into the production process and the interfaces have to be coordinated and adapted precisely. A specific application for cleaning gearbox components of electric vehicles illustrates the key aspects of this process.
Parts cleaning system as an element of the complete production line
BvL Oberflächentechnik from Emsbüren in Germany supplied a Yukon continuous cleaning system for a general contractor’s complete production line. It is used for cleaning ring gear carriers and inner disc carriers after turning. These are components will subsequently be installed in electric vehicles.
The Yukon system provides spray cleaning with flat spray nozzles. For the application at hand, BvL Oberflächentechnik tailored the concept precisely to the customer’s production processes: The cleaning system is seamlessly integrated into the line production with one-piece flow, with a cycle time of only 30 seconds per workpiece. For efficient cleaning, the experts from Emsbüren equipped the transport system with two tracks that can be run independently from one another at different speeds. In this case, one track carries ring gear carriers and the other one inner disc carriers.
Transport system tailored exactly to each application
A portal loader is used for loading and unloading the parts from and into the cleaning system. BvL Oberflächentechnik always tailor their cleaning systems individually to the respective production process and use an intelligent control system to achieve an efficient material flow.
Continuous cleaning process
During the cleaning process, the workpieces continuously cycle through the consecutive treatment zones for cleaning, rinsing, air blast, vacuum drying and cooling. In the cleaning zone, the components move past a nozzle system that was also individually adapted to the parts. In the following zone, the preservative is applied to the parts, which are then blasted with warm air in the air blast zone. In the downstream external Nevada drying chamber, the parts are dried fully using a vacuum drying process. Finally, each part is cooled down to ambient temperature in the Arctic cooling tunnel. At the end of the discharge zone, a special fixture with one scan per track then ensures exact positioning of the portal loader for removing the parts. The portal loader can easily grip the cleaned and dried parts and place them into the next station. The cleaning result then meets the highest requirements for technical cleanliness.
Data collection as a basis for reliable analyses
An excellent cleaning result is no longer enough today, though – process data collection and documentation are also required. The reason: Users now want to be able to see exactly how and with which parameters the process was executed. To achieve this, BvL Oberflächentechnik equipped the cleaning system with a modern interface communication element. It is also connected to the customised mobile data collection system through hardware and software. Information is collected at the cleaning system, evaluated and provided to the user. A configured interface provides communication with a database server on the customer’s network. This achieves full transparency and data are available in real time, offering an ideal basis for reliable production analyses.
With its own experts for automation and software programming, BvL Oberflächentechnik can easily meet the customer-specific requirements for the IT interfaces and databases. That also applies to connecting to upstream and downstream systems, but in particular to higher-level IT systems.
This application illustrates: With its longstanding experience in cleaning components for automotive engineering, BvL Oberflächentechnik also has extensive know-how regarding parts cleaning in electromobility. With their efficient products and solutions, the experts from Emsbüren are ready for new challenges in a sustainable world.
BvL Oberflächentechnik GmbH is one of the largest suppliers of water-based industrial cleaning systems in Germany. As a system partner, BvL offers comprehensive customer solutions through integrated services – from compact washing units and filtration and automated solutions to complex large projects with process monitoring, always complemented by reliable service. BvL currently has around 160 employees. In terms of exports, the company has expanded its position on an international scale, and can rely on an extensive sales and service network in 20 countries.
Contact:
BvL Oberflächentechnik GmbH
Grenzstr. 16
48488 Emsbüren, Germany
Tel.: +49 5903 951-60
Fax: +49 5903 951-90
Press Release:
Christine Brühöfner
Marketing
Tel.: +49 5903 951-509
Fax: +49 5903 951-90
christine.bruehoefner@bvl-group.de
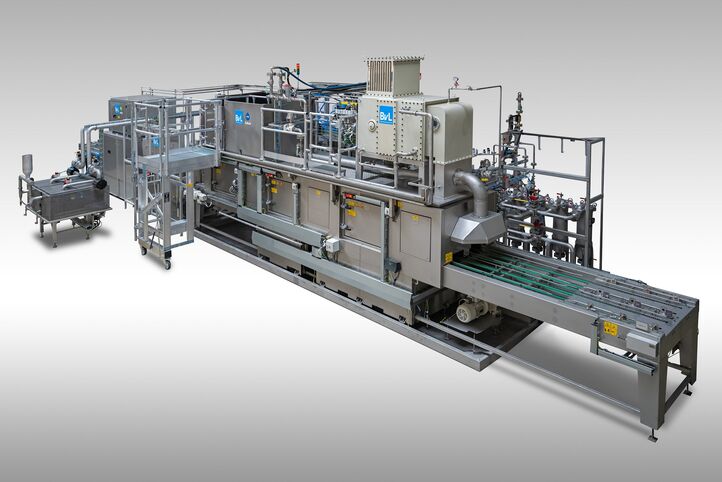